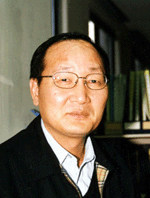
가스나 물 등의 유체를 넓은 지역에 분포된 다수의 사용처에 동시에 효과적으로 수송하기 위해서 배관망을 사용한다. 폴리에틸렌(polyethylene: PE) 관은 저압으로 수송되는 도시가스의 주 배관으로서 정착되었으며 최근 들어 고품질 PE 소재의 실용화에 힘입어 중압으로의 사용이 확대되는 추세에 있다. 가스나 물 등 유체의 수송압력은 안전성 및 경제적 측면에서 매우 중요하다.
1965년경 PE배관이 도입된 이래로 안전성을 바탕으로 수송압력을 증가시키기 위한 노력의 결과, 융착접합기술, 융착장비 분야에서는 적지 않은 성과를 거뒀다.
폴리에틸렌 관은 금속배관에 비해 내식성, 내구성, 유연성, 시공의 편리성, 안전성, 경제성 등의 장점으로 인해 중압 이하의 배관망에서 금속배관을 대신해 주 배관으로 자리를 잡고 있다. 폴리에틸렌 관은 전 세계적으로 저압은 물론 중압(10 bar 미만) 배관으로 사용이 급증하고 있으나 금속배관에서와 같이 배관망의 안전성을 효과적으로 검증할 수 있는 보편화된 비파괴검사기술이 아직 실용화되지 못하고 있어 시급히 해결해야 할 과제로 대두되고 있다.
■ 폴리에틸렌 배관
쪾배관용 폴리에틸렌 소재
폴리에틸렌(polyethylene: PE)은 염화비닐(polyvinyl chloride: PVC)과 더불어 세계에서 가장 널리 보급된 합성 고분자 물질 중의 하나로서 1930년대 영국의 ICI(Imperial Chemical Industries)사에 의해 저밀도 폴리에틸렌(low density polyethylene: LDPE)으로 처음 합성되었다.
그 후 석유화학공업의 발전과 더불어 가공성, 강인성, 화학적 안전성, 전기 절연성, 경제성 등의 우수한 물성으로 인하여 가정용품에서 압력용 배관에 이르기까지 그 용도가 다양하여 수요가 급격히 증가하여 왔다.
압력배관용으로는 1965년경 영국에서 제1세대 소재인 고밀도 PE40(후에 PE63)을 처음으로 사용하기 시작해 1976년에 제2세대인 PE80, 1984년 제3세대인 PE100 그리고 2000년도에는 국내의 삼성종합화학에 의해 고품질(high performance) PE112가 개발되었다.
현재 미국 및 유럽에서는 가스배관용 소재로 제3세대 HDPE(high density polyethylene)인 PE100을 사용하는 추세이나 국내에서는 제2세대 MDPE인 PE80을 사용하고 있다.
쪾폴리에틸렌(PE) 배관설계
폴리에틸렌 배관의 수명은 폴리에틸렌 물성, 매설환경, 내부압력 등에 의존하며 일반적으로 20℃, 최대허용압력(MAOP)에서 적어도 50년을 견딜 수 있도록 설계된다.
쪾폴리에틸렌 배관 사용현황
아래 그림은 1965년 이래로 전 세계적으로 폴리에틸렌 배관의 사용추세를 나타낸 것이다. 1970년대 PE80 중밀도 폴리에틸렌(MDPE) 소재개발로 가스관 시장이 개척되고 1980년대 전기융착(electro-fusion) 기술도입과 PE100 고밀도 폴리에틸렌(HDPE) 소재 개발 등으로 가스관 사용이 급격히 증가하고 수도관으로 사용되기 시작하였다. 1990년대에는 폴리에틸렌 관이 유럽 및 미국을 중심으로 중압 가스배관으로 본격적으로 사용되었으며, 우리나라 및 일본에서는 1990년대 들어 저압용 도시 가스배관으로 사용이 보편화되었다.
쪾폴리에틸렌(PE) 배관의 접합
폴리에틸렌관이 도시가스 배관 시스템으로 구성되기 위해서는 금속배관망과 마찬가지로 배관들이 서로 접합돼야 한다. PE관의 접합은 금속용접과는 달리 접합부내에 타 재질을 사용하지 않고 모재를 사용해 이음매(joints)를 만드는 매우 유익한 방법이다. PE관 접합의 종류는 크게 융착접합과 기계적 접합으로 구분할 수 있다. 융착접합은 접합대상부를 가열·용융·압착하여 냉각·고상화 시킴으로서 일체화하는 방법이다. 기계적 접합은 O-링이나 고무 링 등의 씨일(seal) 혹은 조일 수 있는 재료를 이용하여 기밀성을 확보하는 방법이다. PE관의 가장 대표적인 접합법은 맞대기 융착(Butt Fusion)과 전기융착(Electrofusion)이다.
● 폴리에틸렌 배관의 비파괴 검사
쪾폴리에틸렌 배관의 융착접합부 검사
PE 배관의 안전성은 배관자체보다는 배관들을 서로 연결하여 주는 융착접합부의 성능에 의존한다.
금속배관의 경우 비파괴 검사법이 체계적으로 규정화되어 있어 용접부의 품질성능을 비파괴적으로 평가하는데 효과적으로 사용되고 있으나, PE 배관의 경우에는 <표-2>에서 보는 바와 같이 단순 외관검사를 제외하고는 융착성능을 검증할 수 있는 체계화된 검사기법이 없는 실정이다.
현재 PE배관 융착 접합부의 품질성능 판정은 융착장비에 기록 혹은 표시되는 융착공정 인자들을 확인하는데 의존하고 있다. 지금까지 중압용 고품질 소재가 상용화되었음에도 불구하고 국내에서 PE관의 중압사용에 있어서 가장 큰 장벽은 융착접합부 성능을 평가할 수 있는 검사기술 부재에 있다는 사실이다.
쪾PE배관 비파괴 검사기술 필요성
1) 폴리에틸렌 배관의 사용량 증가
- 금속배관에 비해 내부식성, 내구성, 유연성, 작업성, 경제성이 우수
- 중·저압의 매설용 도시가스 및 상수도 배관으로 사용의 보편화
2) 대구경 배관에서 융착결함 발생될 개연성 증가
- 국내에서는 이음관 관경이 400mm까지 사용되나, 일본은 200mm이하, 미국·유럽에서는 100mm이하가 주로 사용됨
- PE 배관은 관경이 클수록 배관의 진원이 타원(oval)으로 변형되기 쉬우며, 시공 시 PE배관의 정렬불량(misalignment)이 상대적으로 심하게 나타남
3) 비파괴검사기술의 부재
- PE 배관의 안전성은 배관자체보다는 융착접합부의 성능에 의존함.
- 금속용접부의 성능은 일반화된 비파괴검사법으로 검사되지만 PE 배관 융착부의 검사는 규격화된 비파괴검사기술의 부재로 단순외관검사, 융착 조건 확인, 기밀시험에 의존함
- 특히 큰 구경의 배관에서 외관검사 및 기밀시험은 융착성능이나 내부 융착 결함에 대한 정보를 주지 못함
쪾PE 배관 융착접합부 검사기술 동향
현재 금속용접부에 보편적으로 사용되고 있는 비파괴 검사기법은 방사선 시험(Radiography Testing: RT)과 초음파 시험(Ultrasonic Testing: UT)이다. 초음파시험은 인체에 무해하고 작업이 간단해 전 세계적으로 사용이 증가하는 추세다. PE 배관의 경우 금속에 비해 방사선의 투과강도 차이가 크지 않아 융착결함의 판독이 쉽지 않으며, 또한 초음파를 적용할 경우에는 PE 재질의 높은 초음파 감쇠로 인해 기존 금속에 사용하는 초음파 시험법을 그대로 적용하는 것은 한계가 있어, 최근 기술은 PE 전용 초음파 시험에 초점이 맞추어져 있다.
(1) 버트 융착접합부 검사기술
· 초음파 사각 탐상법
- 1980년대 중반 미국의 GRI(Gas Research Institute)에서 금속배관 용접부 검사에 적용하는 기존의 초음파 사각탐상법을 이용하여 버트융착접합부에 존재하는 결함을 검출하는 기술이 개발됨
- 미국 McElory Manufacturing Inc.에서 PE 배관 전용 초음파 장비를 상용화했으며 Oklahoma Natural Gas 사 등 일부 도시가스사에서만 기술을 적용하고 있다.
- 원리적으로 버트 융착결함을 검출할 수 있으나, 측정 및 신호 해석이 어렵고 불감지역(Dead Zone)이 존재하며 분해능이 낮은 단점을 지녀 보편화에 한계가 따른다.
· 초음파 비행 회절 시간법(Time of Flight Diffraction : TOFD)
- TOFD 기법은 결함에서 반사된 신호의 크기(echo 높이)보다는 결함의 선단에서 회절 된 낮은 증폭의 회절신호의 시간차를 이용해 결함의 위치, 분포 및 크기에 관한 정보를 정확하게 얻을 수 있다.
- TOFD 기법은 금속용접부의 결함검출에 널리 사용되며 방사선 검사를 대신할 수 있는 방법으로 각광을 받고 있다. 최근에는 폴리에틸렌 배관 버트융착부 검사에 활용되고 있다.
- 유럽 및 북미 도시가스사에서 버트융착부 검사에 활용
(2) 전기융착부 검사기술
· 초음파 수직 탐상법
- 최근 일본 오사가가스에서 개발한 기술로서 범용 초음파 탐상장비와 이음관 전용 탐촉자를 사용하여 A-scan 방식으로 EF 접합부의 결함을 검출하는 방법.
- 초음파 탐촉자는 점 집속형으로서 음향정합을 향상시키기 위해 PE 재질로 된 쐐기와 폴리머 진동자를 사용함.
- 원리적으로 이음관 두께에 따라 센서가 달라져야 하며, 열선의 굵기 및 간격에 따라 초음파 신호가 달라지기 때문에 측정 및 신호해석이 어려우며 열선 밑의 결함은 검출이 불가능함.
· 배열 초음파 탐상기법
- 한국가스안전공사와 인디시스템(주)이 공동으로 개발한 기술로서 의료용 초음파 진단장비와 같이 초음파 위상배열기법을 이용해 PE 전기융착부 결함을 실시간 영상으로 검출하는 첨단기술
- 진동자가 96개 정도 배열된 초음파 센서를 사용하며 영상을 통하여 융착 접합부내에 존재하는 기공, 불순물, 열선변형(위치, 크기, 간격) 등을 측정할 수 있다.
- 1mm 이상의 기공이나 불순물을 검출할 수 있으며 측정 및 영상해석이 간단해 현장에서 사용이 가능한 휴대용 장비를 최근 인디시스템에서 세계 최초로 개발·실용화 했다.
■ PE 배관의 초음파 탐상기법
쪾 범용 초음파와 배열 초음파 탐상기법
초음파를 이용해 시편내부의 결함을 검출하는 기법으로는 이미 알려진 A-scan, B-scan 과 C-scan 등이 있다. A-scan은 초음파 센서를 특정위치에 고정하고 초음파를 송수신해 초음파의 반사신호를 관찰함으로서 결함의 존재여부와 위치를 확인하고 분석을 통해 결함의 종류 및 크기를 평가한다. B-scan은 한 개의 초음파 센서를 기계적으로 이동시키면서 시편의 내부에서 반사되어온 여러 개의 A-scan 신호를 모아 각 신호의 전파시간에 따른 신호의 세기를 적절히 나타내고 이를 초음파 송수신자의 위치에 따라 표시함으로 2차원 초음파 영상을 만드는 것이다.
최근에는 위상배열 초음파기법을 비파괴 검사에 도입하고 있다. 이것은 산부인과에서 태아의 모습을 실시간 초음파 영상으로 보여주는 원리와 같다. 보통 실시간 초음파 영상에 사용되는 초음파 배열 탐촉자는 수십 개 또는 수백 개의 미소 초음파 센서로 구성되며 각각의 미소센서는 독립적으로 초음파를 송수신할 수 있도록 되어있다. 각각의 미소 초음파 센서를 통해 초음파를 송수신하기 위해서 수십 개의 독립된 초음파 송수신회로를 가진 시스템을 사용한다.
(주)인디시스템에서 개발한 AIM33인 배열 초음파탐상시스템은 16개의 독립된 초음파 송수신회로를 가지고 있으며 최고 98개의 미소센서를 가진 초음파 배열탐촉자를 연결해 실시간 영상을 획득할 수 있게 하는 시스템이다. 그리고 중심주파수가 7.5MHz, 5MHz, 3.5MHz인 3 종류의 배열 탐촉자를 이용하여 영상을 획득한다.
쪾 인공시험편에 대한 배열 초음파 영상
· 시 험 편 : 정상융착 시험편, 융착결함이 있는 시험편
· 측정장비 : AIM33 (인디시스템의 배열초음파 검사장비)
· 사용주파수 : 5MHz (배열초음파 센서)
· 초음파 영상결과
- 정상융착과 비정상융착의 차이는 열선 바로 밑에 존재하는 이음관 내면과 PE배관 외면이 접하는 계면의 존재유무임
- 정상융착일 경우에는 열선영상만 나타나지만 융합불량이 존재할 경우에는 열선영상 바로 밑에 융합결함(lack of fusion)을 지시하는 영상이 나타남
쪾 배열 초음파의 현장시험
(1) 현장의 불량 융착부
· 시 험 편 : 현장에서 절단한 관경 250mm, 350mm의 불량 융착부
· 측정장비 : AIM33 (인디시스템의 배열초음파 검사장비)
· 사용주파수 : 5MHz (배열초음파 센서)
· 초음파 영상결과
- 열선의 영상을 나타내는 열선지시 바로 밑에 융합불량의 존재를 암시하는 나타내는 융합불량(lack of fusion) 지시가 점선형태로 나타남.
- 융합불량지시의 길이에 대응하는 길이만큼 융합이 되지 않음.
- 열선지시와 융합불량지시 사이만큼 융합이 되지 않고 간극형태로 존재
· 융합불량원인 : 배관자체의 진원변형 및 배관의 정렬불량(misalignment)에 의한 배관외면과 이음관 내면사이의 간극 불균일
(2) 가스 누출된 PE 배관 융착부
· 시 험 편 : 10년 정도 사용 중인 관경 200mm의 폴리에틸렌 배관으로서 사용 중 가스누출로 인하여 굴착하여 절단한 융착결함이 있는 접합부
· 측정장비 : AIM33 (인디시스템의 배열초음파 검사장비)
· 사용주파수 : 5MHz (배열초음파 센서)
· 초음파 영상결과
- 폴리에틸렌 배관 외면과 이음관 내면사이의 간극이 작은 융착부에 대한 배열 초음파 결과에서는 정상적으로 융착이 되었음을 지시하는 열선 영상들이 거의 등 간격으로 관찰됨.
- 접합부에서 간극이 큰 융착 접합부에 대한 배열 초음파 결과에서는 열선지시들이 불규칙하게 관찰되며 열선지시 바로 밑에 융합불량의 존재를 암시하는 결함지시들이 관찰됨. 융착부의 일부분은 붙어 있으나 대부분은 떨어져 있으며 이들 부분에서 열선지시들과 결함지시 사이에는 3-4mm 정도의 간극이 존재함을 알 수 있다. 이 결과들은 결함융착부의 단면과 일치함을 알 수 있다.
쪾 가스누출 사고원인
- 사고 융착부에는 배관 삽입불량과 융합불량이 존재함.
- 배관 삽입불량은 배관을 이음관에 삽입시 한쪽 배관은 깊이 들어가고 반대편 배관은 적게 들어감
- 융합불량은 배관의 진원변형 및 배관의 정렬불량(misalignment)에 의한 배관외면과 이음관 내면사이의 간극 불균일로 인하여 간극이 작은 부분은 정상융착이 되었으나 간극이 상대적으로 큰 부분에서는 융착시 용융이 간극을 채우지 못하여 결함이 발생됨
- 융착시 결함의 폭이 큰 융합불량이 존재하였으나 융착부의 일부분은 융착이 되어 있어서 건설 당시 기밀시험을 통과하였을 것으로 판단됨.
처음은 가스가 누출되지 않았으나 약 10여년 가까이 사용하면서 내압 및 외부하중에 의해 결함성장으로 누출이 발생된 것으로 판단됨.
(3) 새들 융착 접합부
· 폴리에틸렌 주배관 및 분기배관
- 아파트에 도시가스를 공급하기 위하여 기존에 매설되어 있는 폴리에 틸렌 주배관(관경 350mm, 공급압력 3.5 bar)으로부터 분기작업
- 분기배관 연결을 위하여 3개의 새들 융착 접합부(Saddle Fusion Joints: SFJ)와 3개의 전기융착접합부(Electro Fusion Joints: EFJ)를 사용함.
- 새들 융착 접합부(SFJ)의 건전성 평가를 위하여 배열초음파 기법사용
- 주배관의 관경(350mm), 도시가스공급압력(3.5bar)
· 새들 융착부에 대한 배열 초음파 탐상
- 탐상대상 : 새들 융착 접합부(SFJ1, SFJ2, SFJ3)
- 탐상장비 : 배열 초음파 검사장비(인디시스템 AIM33), 배열초음파센서 (7.5MHz)
- 탐상방법 : 접합부 양쪽에 금속밴드가 부착되어 있는 부위를 제외한 접합부에 대하여 배열초음파 탐상을 실시하여 4지점에 대하여 초음파 영상을 획득
- P1, P2, P3, P4는 배열초음파 영상을 측정한 위치를 의미함
- 새들 융착 접합부에서 융착결함을 암시하는 지시는 관찰되지 않음
■ 결론
배관망의 안전성은 배관자체의 품질뿐만 아니라 배관과 배관을 연결하는 접합부의 품질성능에 크게 의존한다.
폴리에틸렌 배관은 금속 배관에 비해 내식성, 내구성, 유연성, 시공의 편리성, 안전성, 경제성 등의 장점으로 인하여 중압이하의 도시가스 및 상수도용 배관으로 자리 매김하고 있으나, 고압적용이 어렵고 변형이 쉬워 현장에서 융착 접합부의 품질성능을 검사할 수 있는 보편적인 비파괴 검사기술이 없다는 것이 단점으로 지적되어 왔다.
현재 융착조건의 확인 및 기밀시험에만 의존하는 검사방법으로는 폴리에틸렌 배관 접합부의 품질성능을 검증하는 데에는 한계가 따른다.
최근 들어 유럽에서는 초음파의 비행 회절 시간(TOFD) 기법을 이용하여 버트융착 접합부를 검사하고 있으며, 국내에서는 배열초음파 기법을 이용하여 전기융착 접합부를 검사하는 기술을 실용화 하였다.
이 기법들은 측정결과를 2차원 영상으로 표시하고 현장에서 거의 실시간으로 폴리에틸렌 배관 접합부의 융착성능을 효과적으로 검사할 수 있는 기술로서 배관망의 안전성을 크게 향상시킬 것으로 생각된다.
한국가스안전공사에서는 폴리에틸렌 배관의 전기융착 접합부에 대한 검사기술을 실용화해, 검사기술의 검증을 현장시험을 수행 중에 있다.