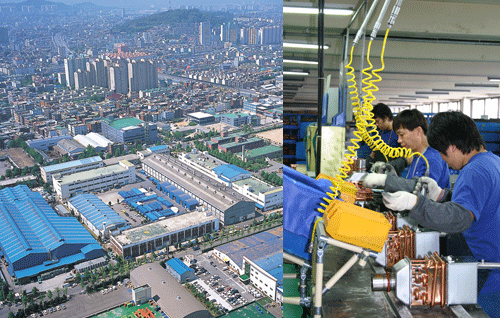
1973년 롯데계열사 중 4번째로 설립된 롯데기공은 82년부터 가스보일러 사업을 시작했으며 85년에는 국내 최초로 국산 가스보일러를 생산했다. 1987년에는 국내 최초로 KS마크를 획득, 가스보일러 선구자의 역할을 했다. 1990년에는 프랑스의 SAUNIER DUVAL社와의 가스보일러 기술 제휴를 통해 보일러 제조기술의 선진화에 기여했으며 95년 가스보일러 부문 ISO인증, 사후봉사 우수기업(A/S)마크 표시 인증을 획득, 고객만족의 밑거름을 다졌다.
97년 4월 남미와 우루과이에 가스보일러를 첫 수출하는 쾌거를 올리며 해외시장에 진출한 롯데기공은 98년 칠레, 우루과이, 뉴질랜드에, 99년 카자흐스탄, 중국에 수출, 수출국을 다변화했다. 2004년 아르메니아 현지 JVC(합작투자법인) 설립, EUROTERM社와 SKD방식으로 계약을 체결하기도 했다.
롯데기공은 대표 브랜드였던 일반형 보일러 ‘16비트’는 1999년 출시했으며 이후 2002년 HI-Q, 2004년 HI-Q 200·300, 2005년에는 ‘하이큐 콘덴싱 10+’를 출시했다.
2003년 한국능률협회가 주관하는 ‘대한민국 생산혁신 대상’, 2004년 한국표준협회 주관 한국서비스대상 ‘최우수상’을 수상한데 이어 올해까지 3년 연속 수상했다. 또 ‘대한민국 가치창조 기업대상’과 ‘에너지 위너상’을 수상하는 성과도 올렸다.
Cell 생산으로 생산성 UP
초기에 Conveyor방식으로 가스보일러를 생산했던 롯데기공은 콘베이어 생산방식의 문제점을 발견하고 Cell 생산 방식을 도입하게 된다.김창연 생산본부장은 “콘베이어 생산방식은 과잉생산, 생산대기, 운반, 가공, 재공, 동작, 불량 및 수리 등의 7가지 LOSS가 발생하고 분업에 의한 라인 밸런스가 맞추기가 어려웠다”라며 “또 근속 연수에 따른 생산성 향상을 기대하기 어렵고 보람 및 달성감에 대한 직장 MORAL이 저하된다”며 Cell 방식 도입 배경을 설명했다.
2002년 1차로 2개 콘베이어 라인과 저탕형 생산라인을 철거한 곳에 8개의 Cell 라인을 설치, 콘베이어와 Cell 라인을 공존했으나 2004년에는 1층에 있던 8개의 Cell 라인을 2층으로 옮기면서 추가로 8개의 라인을 더 설치해 총 16개의 Cell 라인을 구축했다.
Cell Line 방식 도입은 품질측면에서는 소그룹(3인) 책임생산과 검사자 이름을 명기한 실명제 검사, 부품 SET화 공급(1대차 6SET분)으로 부품 오조립 및 결품 요인을 제거할 수 있어 제조 품질을 확보할 수 있었다. 납기측면에서는 최대 16기종을 동시에 생산할 수 있고 최소수량 6대를 생산할 수 있어 소량 단납 대응이 가능해졌다. 이로써 1인당 생산량이 18% 증가했으며 대당 조립공수가 절감되고 수요변동에 따른 생산 LOSS가 줄어들어 총 23%의 생산성 향상을 가져왔다.
가스보일러 국내 최초 국산화·KS 획득
16개 Cell Line 구축… 생산성 23% UP
하루만에 개선한다
롯데기공 생산본부에는 ‘개선활동위원회’라는 별도의 조직이 있다. 개선활동위원회는 공장 전체의 개선활동을 체계적이고 지속적으로 지원함으로써 개선활동의 활성화를 기하고 스스로 개선하는 공장을 만들기위한 목적으로 조직됐다. 현재 제2기 개선활동위원회가 출범해 운영되고 있으며 생산본부의 김관영 부장이 본부장으로 전문위원 및 위원 등 총 6명으로 구성됐다.김관영 부장은 “개선활동위원회는 공장 전체의 개선활동 계획수립 및 활성화 방안을 연구하는 곳으로 개선활동 현황 관리 및 홍보와 ‘자율개선팀’ ‘일일개선팀’ 등 개선활동을 지원하고 있다”며 “제1기 활동으로 일일 45팀, 자율 9팀을 지원했으며 개선테마 99건을 완료해 연간 5,000만원의 원가절감효과를 봤다”고 밝혔다.
일일개선팀은 조립공정, 부품이송, 제품보관 등 공정에서 발생하는 낭비요소를 찾아 제거해 효율적인 생산공장을 스스로 만들기위한 것으로 주1회 1팀이 구성돼 하룻동안 자신들이 정한 개선테마를 개선한다. 일일개선팀 활동 참여자는 다른 업무활동이 금지되고 오직 일일개선팀 활동만 할 수 있다.
팀별, 조별 자율적으로 개선팀을 구성해 팀내의 낭비요소를 제거하는 자율개선팀은 최대 5명 이하로 구성되며 정규근무시간 이외에 활동한다. 물론 잔업 및 특근도 가능하다.
전담관리제로 효율성 제고
고품질만이 생존시대에서 협력사와 윈-윈 할 수 있는 전략을 고민하던 롯데기공은 ‘협력업체 전담관리제’를 도입했다.김창연 본부장은 “반복적이고 동일공정불량이 발생하고 수입검사, 공정검사의 한계, 적극적 업체지도를 통한 사전품질 관리를 위한 것”이라며 전담관리제 도입배경을 밝히고 “중요 관리부품 생산업체를 대상으로 월2회 방문해 품질 데이터를 기초로 품질개선 방안을 설계하고 작업표준화 및 검사설비 개선을 지원하고 있다”고 말했다.
‘전담관리제’를 운영하기 전인 2004년 약 1,000여건의 공정불량이 났으나 2005년에는 약400여건으로 줄었으며 불량률도 실시전대비 50%이하로 감소했다.
또 협력업체와 모기업의 수평적 업무 커뮤니케이션으로 창의력을 바탕으로 한 품질향상과 원가절감, 공정개선 등에 의한 상호 이익 극대화를 위해 ‘협력업체 제안제도’를 실시하고 있다. 생산본부의 전 협력업체가 대상이며 활성화를 위해 협력업체 평가시 우수등급을 부여하고 간담회시 포상을 실시하고 있다. 제안자에 대해서는 본사 규정에 의거한 동일 인센티브도 지원하고 있다.

▲ 좌측부터 전시장, 검사를 수행하고 있는 직원
보일러업계 ‘벤츠’ 지향
롯데기공의 보일러 부문 주력 제품은 ‘Hi-Q 콘덴싱 10+’와 ‘Hi-Q 200’이다. 전모델에 대해 고효율기자재 인증을 받은 ‘Hi-Q 콘덴싱10+’는 기존 콘덴싱 보일러와 차별화된 최고 성능의 명품 보일러를 표방하고 출시됐다.이돈형 부장은 “유럽이나 선진국에 수출했을때 ‘인정받을 수 있는 보일러인가?’를 고민했다”라며 “내구성과 성능이 보장되지 않고서는 선택받기 어려운 시장에서 제품의 자체 성능으로 경쟁할 수 있는 시장 조성이 돼야 한다”고 말했다.
국내 최초로 현열과 잠열 열교환기 모두를 습기에 강한 스텐레스로 제작한 것이 특징인 ‘Hi-Q 콘덴싱10+’는 10년 이상 오래 쓸 수 있는 내구성이 뛰어나다. 특히 유럽 최신기술을 채택한 일체형 열교환기이면서 Door Open 구조로 돼 있어 쉽게 열교환기를 분해, 청소할 수 있어 연소에 사용되는 공기의 먼지로 인한 막힘 현상을 완벽하게 방지하고 열효율을 처음 구입할 때와 10년 후에도 똑같이 유지할 수 있다. 또한 국내 최초로 코일형 열교환기로 연소의 최적화를 달성하므로써 최고 30%의 가스비를 절감할 수 있는 고효율 보일러다.
끊임없는 R&D
롯데기공은 부설 냉열기기 기술 연구소를 개설 운영하고 있다. 40여명의 전문 연구 인력을 보유하고 있다. 연구 개발 수행 방향은 크게 가스기기(가스보일러 등)사업과 냉기 부분 사업(쇼케이스·자판기 등)으로 나뉜다.김창연 본부장은 “가스기기 사업과 관련해 주요 개발 추진 방향은 정부의 에너지 정책과 맥락을 같이하는 가스보일러의 고효율화 및 콘덴싱 가스보일러 개발”이라며 “소비자에게 보다 편리하고 친숙한 제품을 개발하기 위해 홈네트워킹 SYSTEM과 연계되는 가스보일러를 지속적으로 개발할 계획”이라고 밝혔다.
이를 위해 연구원들의 전문 기술에 대한 능력 향상을 위해 전문 위탁 교육 기관에 연수 기회를 부여하고 기술 개발과 관련해 관련 학과에 대한 진학 및 학위 취득을 위한 지원을 아끼지 않고 있다. 또한 산학 협동을 위한 연구 개발 및 전문 기관과의 공동 연구를 통해 좀 더 향상된 기술 연구 및 제품 개발에 힘쓰고 있다.