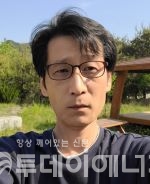
최근 SOFC(고체산화물 연료전지) 업계에는 새로운 사업구조가 형성되고 있다. 기존에는 소재회사로부터 소재를 공급받아 셀, 스택 및 시스템 모 두를 일괄 생산하는 사업구조와 외부 스택을 공급 받아 시스템을 제작하는 사업구조로 나뉘었지만 최근에는 외부로부터 셀을 공급받아 스택과 시스템을 생산하는 구조이며 실제로 이러한 회사들이 빠르게 늘어나고 있다.
그런데 문제가 있다. 셀을 공급할 수 있는 회사는 극히 일부다. 셀 양산화 기술을 확보하기까지는 많은 시간이 필요하기 때문이다. 이유는 셀 제작공정이 도자기 생산기술과 근본적으로 다르지 않고 고온에서 셀을 구워내는 과정을 확인할 수 없다는 데 근본적인 어려움이 있기 때문이다. SOFC용 셀은 크게 전해질 지지형 셀(ESC, Electrolyte Supported Cells)과 연료극 지지형 셀 (ASC, Anode Supported Cells)로 분류된다.
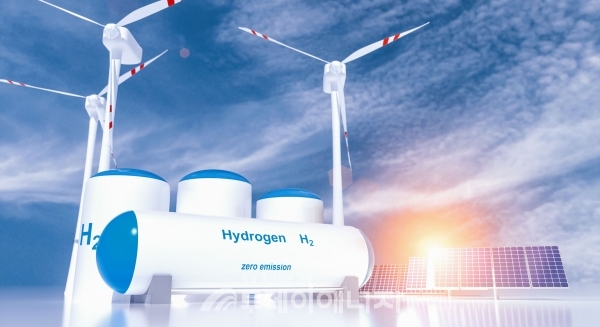
SOFC 의 중저온 구동과 출력밀도(W/cm2) 향상을 위해 현재는 ASC가 더 일반적인 셀로 자리 잡고 있다. ASC의 최대 출력밀도는 2000년까지 1W/cm2를 넘지 못했지만 최근에는 3W/cm2에 근접하는 높 은 성능 수준에 올라왔다. 비약적인 출력밀도 향상의 핵심기술은 전해질 박막화를 통한 셀 저항 감소와 고성능 공기극 (MIEC, Mixed Ionic & Electronic Conductor) 사용에 있으며 전해질의 두께는 10㎛ 전후의 후막에 서 2~3㎛ 정도의 박막화가 이뤄졌다.
초창기에 사용된 LSM 공기극 소재는 단순 전자 전도성 소재로 전해질 소재와 복합 공기극 소재로 적용됐다. LSM을 기반으로 한 복합소재 공기극은 공기, 전자 전도체 및 이온 전도체가 접하는 삼상 계면(TPB, Triple Phase Boundary)에서만 전기화 학반응이 발생하지만 MIEC 공기극을 적용할 경우에는 공기극 표면 전체에서 전기화학반응이 발생 하는 장점이 있다. 그러나 MIEC 공기극 소재들은 전해질 표면에 코팅 후 열처리 단계에서 SrZrO3와 같은 부도체 특성을 갖는 이차상이 발생돼 셀 성능을 크게 저하시킨다. 따라서 이러한 문제를 해결하기 위해서 MIEC 공기극과 전해질 사이에 반응 방지막(Inter Layer)을 추가로 적용하고 있으며 주로 CeO2계 전해질이 적용되고 있다. 반응 방지막 또한 전해질이기 때문에 저항을 낮추기 위해서는 두께를 박막화하고 치밀한 미세구조를 확보해야 하며 MIEC 공기극 적용과 더불어 가장 중요한 기술로 부각되고 있다. 또한 유럽 및 미국을 중심으로 ASC의 연료극 지지체 두께를 줄이고 있다. 셀 성능향상을 위한 목적도 있으나 더 큰 문제는 니켈 가격 상승에 있다.
ASC의 전체 부피 중 90% 이상이 연료극 지지체 이며 연료극 지지체의 50% 이상이 산화니켈(NiO)이다. 전기차의 주행거리 연장을 위해 배터리 양극재 조성이 빠르게 High-Ni 계열(NCM811, LiNi0.8Co0.1Mn0.1O2)로 이동하고 있고 2025년부터 본격적인 도입이 될 것으로 업계에서 보고하고 있다. 따라서 니켈 가격 상승은 계속 지속될 것으로 예상되며 국내에서도 연료극 지지체의 두께를 줄이는 추가 개발이 필요해 보인다.
ESC의 경우에는 가장 저항이 큰 전해질을 150㎛ 정도의 두께를 갖는 전해질 지지체로 사용하기 때문에 저항 감소를 위해 850℃ 이상의 고온에서 작동해야 하는 단점이 있으나 상대적으로 연료극의 두께가 얇아 연료 이용률이 높고 시스템의 효율을 높이는데 유리하다.
ESC 또한 성능 향상이 이뤄지고 있다. 주요 원인은 고이온 전도성 전해질 소재의 개발에 있다. 대표적인 전해질 신소재로서 ScSZ(Sc2O3 stabilized ZrO2)가 있으며 높은 이온 전도도와 대기 중에서 안정적인 성능을 보이는 조성에서 상변태가 발생하는 단점이 있었으나 일본 Toho Gas사에서 상변태 발생이 없는 신소재(10Sc1CeSZ)를 개발해 상용화에 성공했다. 이 소재는 일본 최대 지르코니아 분말 제조사인 DKKK에서 생산 및 보급하고 있고 블룸에너지에도 공급되고 있다.
그러나 환원 분위기에서 Ce4+ 이온이 Ce3+ 이온으로 변하면서 이온 반경이 증가해 전도도의 하락이 발생하는 단점이 확인됐다. 이에 상변태를 억제하면서 세륨(Ce)이 아닌 다른 2차 안정화제가 적용된 ScSZ 신소재 개발이 진행되고 있다. 대표적인 신소재로 Ce 대신 Mg가 치환 고용된 ScSZ(블룸에너지) 그리고 당사에서 개발한 Ce-free ScSZ 전해질이 있다. 국내에서는 최근 전남대학교에서 새로운 ScSZ 전해질 소재를 개발 중이다. 많은 전문가들 중에는 높은 스칸듐(Sc) 가격 때 문에 ScSZ 전해질 사용에 대한 경제성 문제를 제기하고 있다.
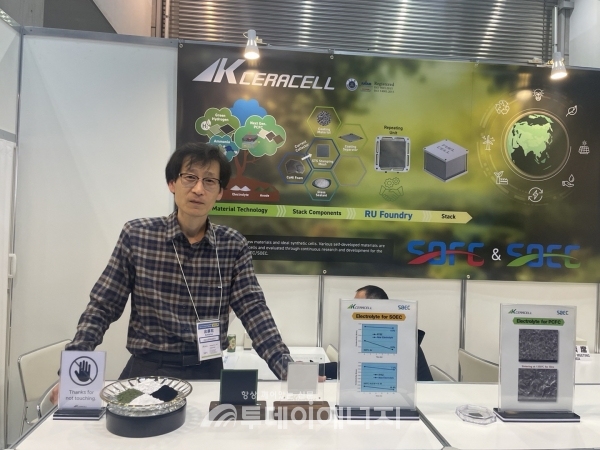
필자는 최근 학술대회에서 ESC와 ASC 생산에 따른 소재 원가를 비교해 발표했다. 동일한 YSZ(Y2O3 stabilized ZrO2) 전해질을 적용할 경우 ESC가 가격 경쟁력이 높다. 이유는 앞서 언급한 것처럼 니켈 가격 상승에 있다. ScSZ 전 해질 가격이 YSZ 대비 2.5배 높다는 가정 하에 비교해도 ScSZ 전해질 기반의 ESC의 가격 경쟁력이 높다. 실제로 현재 Sc 화합물들은 매우 고가이다. 주된 이유는 실제 산업분야에 극히 일부에만 사용 되는 원소이다. 하지만 매장량에 있어서는 Y가 Sc 대비 약 1.25배 정도로 높을 뿐 향후 대량 사용함에 있어 Sc의 매장량은 부족하지 않다.
ScSZ 전해질은 초기 일본에서 활발히 개발을 주도했다. 일본 과학자들은 처음부터 알고 있었던 것으로 생각된다. 이유는 희토류 추출 및 정제 기술은 일본에서 시작되었기 때문이고 Sc의 매장량은 실제로 풍부하다는 것을 가장 먼저 알았던 것으로 보인다. 최근에는 그린수소 생산을 위한 SOEC(고체산화 물 수전해기)용 셀과 암모니아를 직접 연료로 사 용하는 DA(Direct Ammonia)-SOFC용 셀 개발이 활발히 진행되고 있다. SOEC용 셀의 경우에도 ASC 및 ESC 모두 개발 되고 있다. ESC의 경우 Ni depletion 문제 해결이 용이하며 향후 소형모듈원전(SMR)과 연계 운전할 경우 높은 수소 생산효율을 기대할 수 있다.
DA-SOFC는 암모니아를 스택에 공급하기 전에 암모니아 개질기를 통해 분해 후 공급하는 방법과 개질기 없이 암모니아를 직접 스택에 공급하는 방법이 있으며 후자의 경우에는 셀 내부에서 암모니아를 직접 개질할 수 있는 새로운 연로극 소재 등이 개발되고 있다. SOEC 및 DA-SOFC용 셀로서 향후 기대되는 셀은 프로톤(Proton) 전도성 전해질 기반의 셀 (PCFC, Proton Conducting Fuel Cells)이다.
PCFC 는 저온에서 기존 SOFC 대비 높은 이온 전도도를 확보할 수 있으며 PCFC에 사용되는 연료극은 기존 SOFC에 사용되는 연료극 대비 높은 암모니아 분해능을 갖고 있다. 하지만 아직까지 상용화 셀로 인정받는 PCFC용 셀은 없으며 당사에서도 최근 PCFC 개발을 시작했다. 실제 개발을 시작해 보니 주요 문제는 PCFC용 전해질의 낮은 기계적 물성에 있다고 판단하고 있다. 그러나 이러한 문제도 해결될 것으로 기대하고 있다.
SOFC 및 SOEC의 국내 국산화 및 자립화를 위해서는 이제 스택 제조원가를 낮추는 노력이 필요하다. 다행히 금속 분리판 소재는 기존 일본 및 독일 제품 대비 가격 경쟁력이 높은 소재(STS 460FC)를 개발해 상용화를 시작했다. 최근에는 460FC를 이용해 형단조(Stamping) 공 정을 통한 저가 분리판 및 집전체 양산화를 위한 개발이 진행되고 있고 수입에 의존했던 글라스 밀 봉재 또한 국산화 개발이 진행 중에 있다. 스택에 적용되는 핵심 소재부품들의 국산화 및 저가화는 국내 SOFC 및 SOEC 산업발전을 이끄는 토대가 될 것이다.